Make it feasible: Overcoming the 3D printing problem of scale
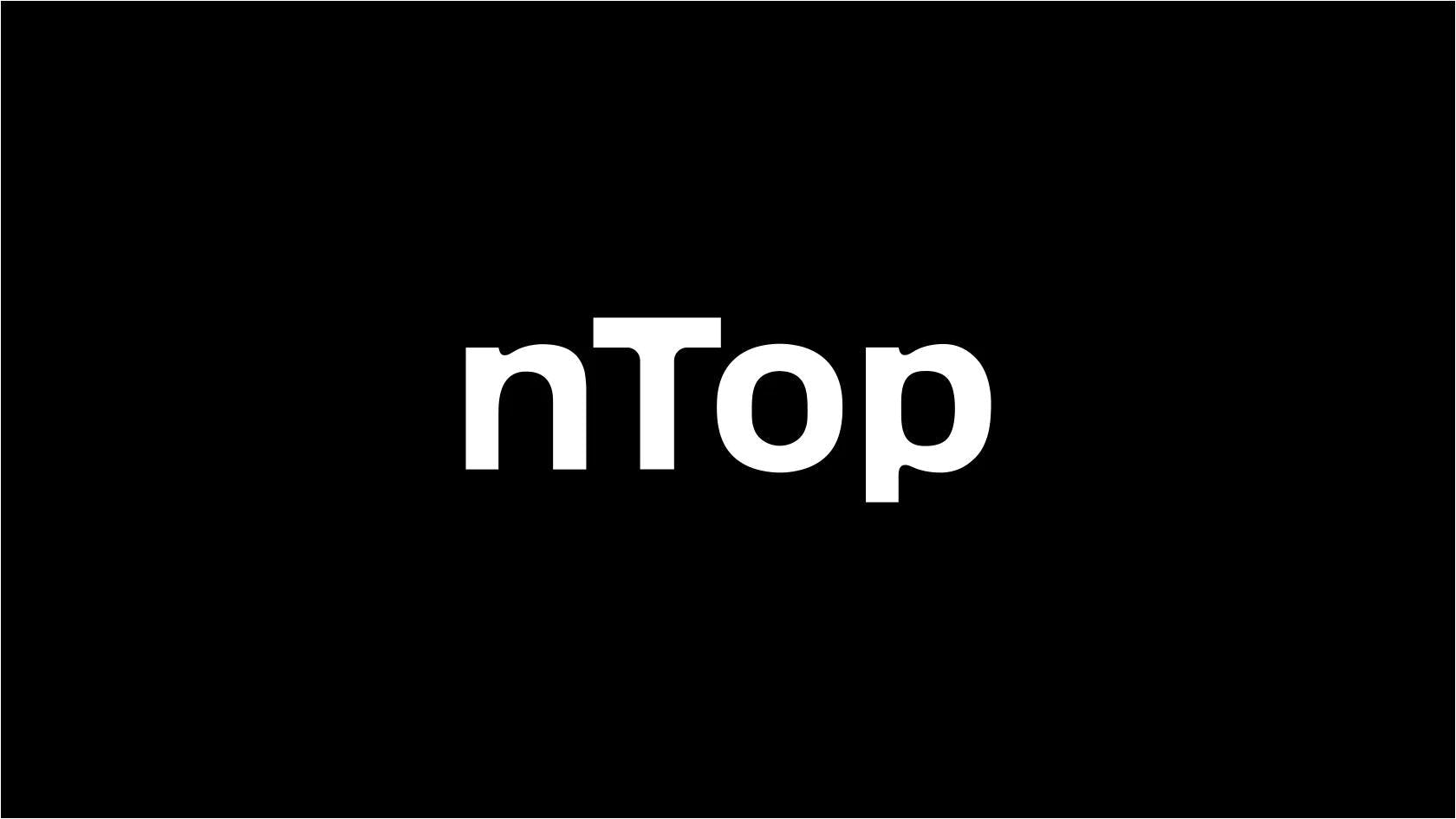
Written by nTop
Published on April 1, 2020
The first NFL Helmet Challenge DfAM eSeries Guest Blog
The entire world seems to be talking about the future (and present) state of health and wellness. Medical devices are one of the most important elements of healthcare and wellness, and the emergence of advanced manufacturing methods like 3D printing are core to the advancement of medical devices and personal protective equipment. The time has never been better suited for the NFL Helmet Challenge aimed at improving football player safety, but is additive manufacturing the right solution to the Challenge?
It seems like a no-brainer that it will play some role in the winning submission. The unrivaled design freedom, the approachability of digital tooling, the next-generation materials… they all point to “yes”. However, there is one dimension to this challenge that 3D printing often struggles at but is simultaneously critical to winning the Contest.
Scalability.
In the Contest Rules on winner selection, the criterion right below the actual Helmet Performance Score is the “submission feasibility for use in the NFL.” This means that just because a physical Contest submission happens to pass all of the physics tests doesn’t mean it’s ready for the National Football League. Can it be repeatably produced? Can it be adjusted to fit all players? Will it be broadly accepted by the teams?
These are all issues of scalability.

Blueprint’s engineers use Design for Additive Manufacturing (“DFAM”) to make parts economically feasible.
Why is it so difficult to build additive parts at scale? There are a few reasons, and in my webinar, I’ll show you the three main pitfalls hindering product developers when implementing 3D printing at volume. I’ll show how identifying and measuring business value, using scalable data management practices, and Design for Additive Manufacturing are all inseparable from scalable 3D printing solutions. Finally, I’ll reveal how Blueprint, coaches our clients on building scalable AM solutions.
To stay up to date on The NFL Helmet Challenge DfAM eSeries click here.

The Six Business Drivers of Additive Manufacturing is a framework for capturing the full value of 3D printing. Download the Little Blue Book of 3D Printing to check out the Six Drivers: additiveblueprint.com.
nTop
nTop (formerly nTopology) was founded in 2015 with the belief that engineers’ ability to innovate shouldn’t be limited by their design software. Built on proprietary technologies that upend the constraints of traditional CAD software while integrating seamlessly into existing processes, nTop allows designers in every industry to create complex geometries, optimize instantaneously, and automate workflows to develop breakthrough parts and systems in record time.