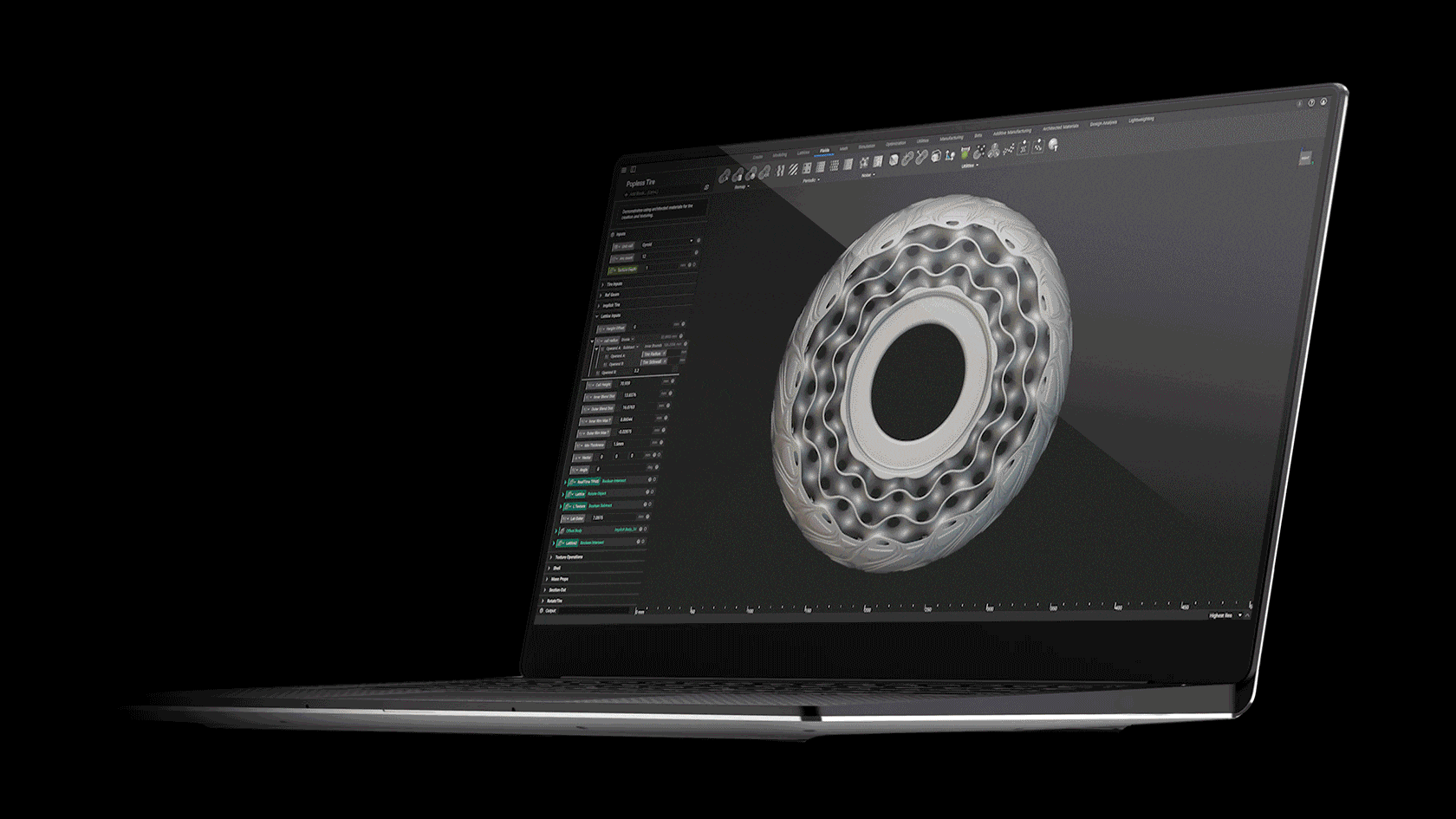
Why use nTop for product design?
nTop enables you to solve complex engineering problems for additive manufacturing.
Speed
Receive real-time feedback and 10x to 100x performance increases because complex modeling operations that take minutes in other software become instantaneous in nTop.
Complexity
Create intricate geometries that would be impossible in traditional CAD, and manage design complexity using math, data, and logic.
Reliability
Build reusable design processes that won't break even when their inputs change, and connect workflows to your existing engineering software stack.
Get your hands on the most powerful design software for additive manufacturing
nTop gives you access to a unique set of capabilities that allow you to transform the way you design, refine, and scale product development.
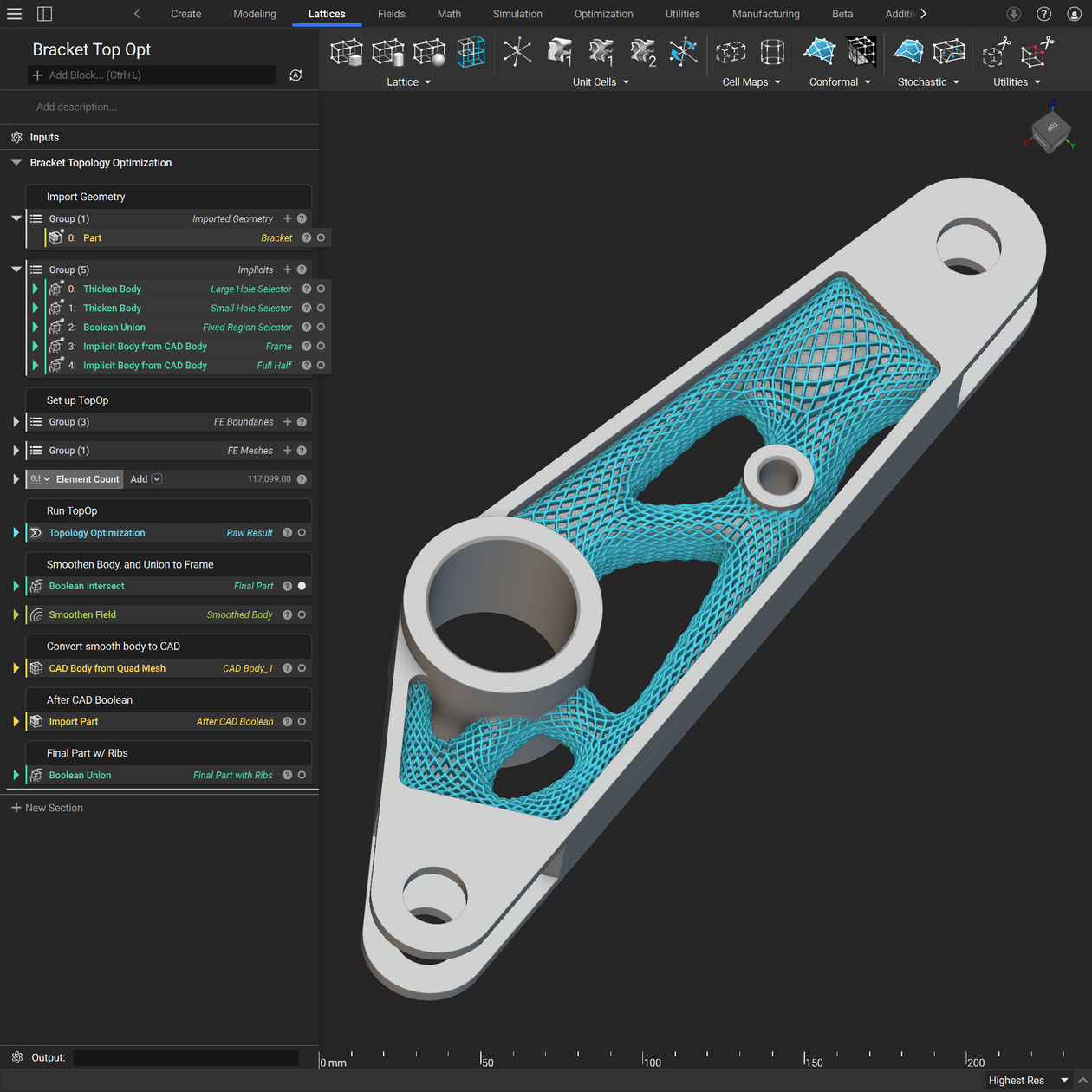
Design
Create unbreakable geometries with our implicit modeling engine. Since every solid body is described as a single mathematical equation, you can adjust and iterate on your designs instantly.
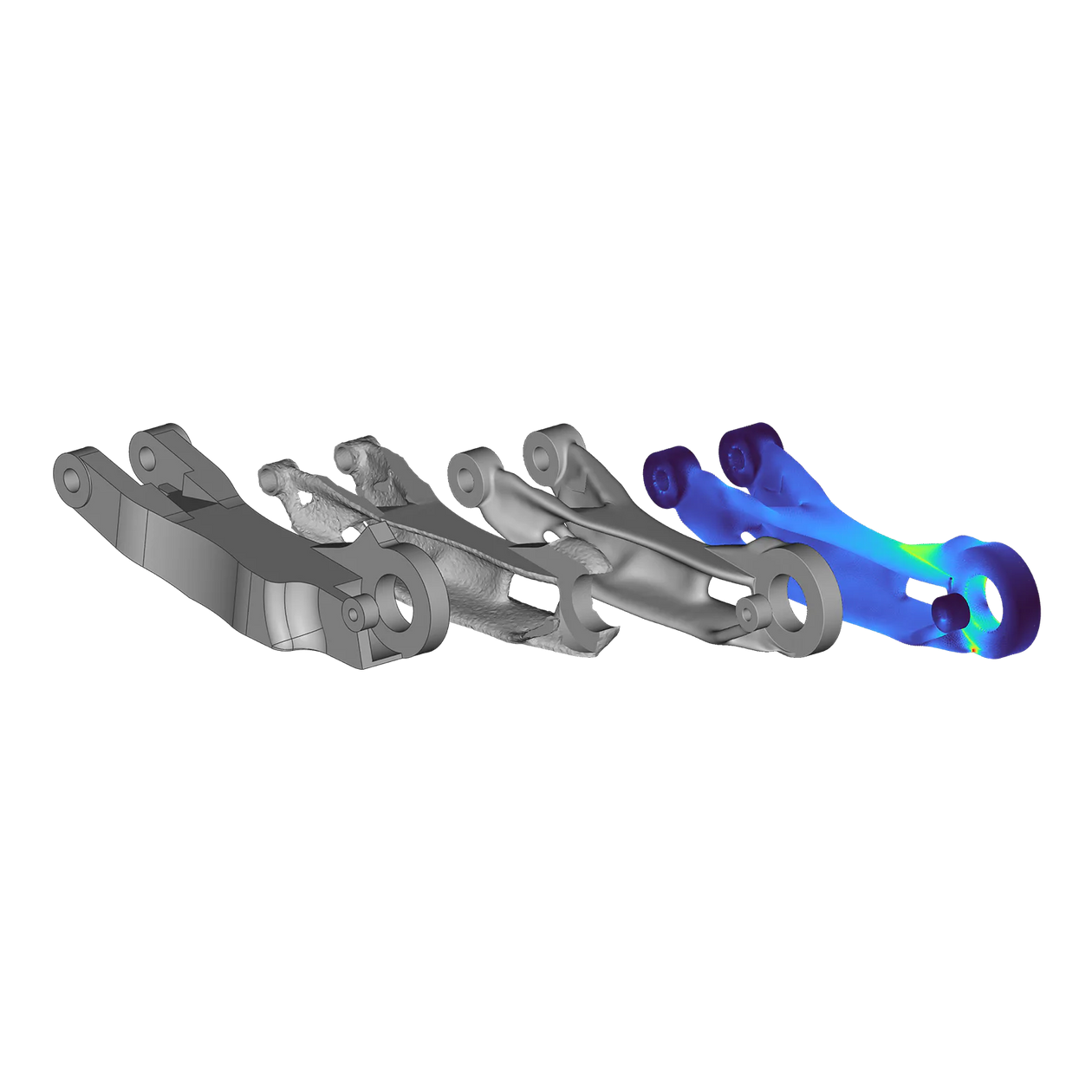
Optimize
Achieve better performance by using Field-Driven Design to optimize based on simulation, test, or analytical data. Take advantage of our best-in-class tools to shorten your design cycles.
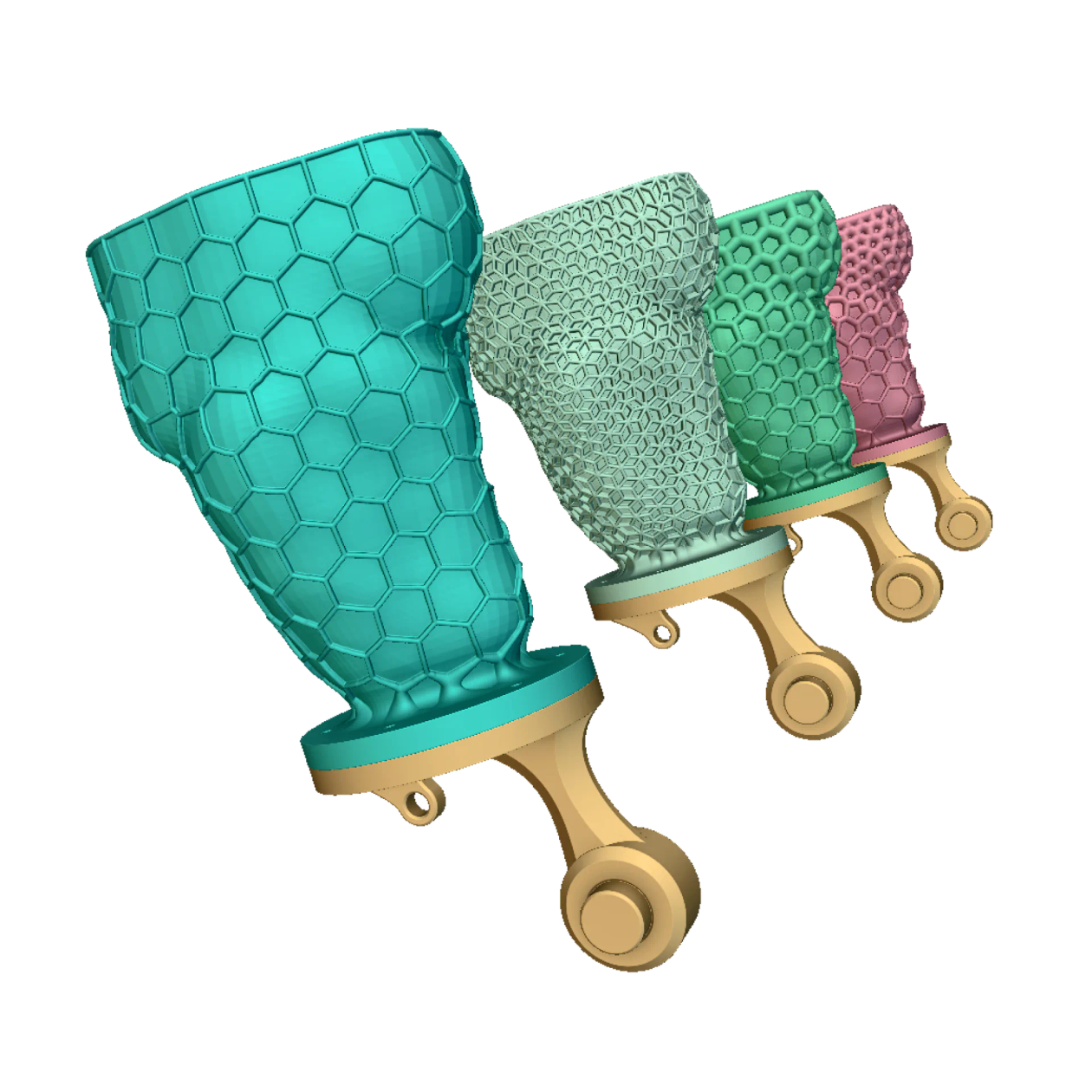
Scale
Create reusable processes to automate repetitive design tasks, batch-process similar parts, and generate multiple design candidates during simulation-driven design.
Software built on transformative technology
Easy in. Easy out.
Seamlessly import and export data within your existing workflows.
Import
Upload CAD files and other engineering data.

CAD
STEP (.step), Parasolid (.x_t and .x_b), CATIA (.CATPart, CATProduct), Solidworks (.sldprt, .sldasm), Creo (.prt, .asm), NX (.prt), Inventor (.ipt, .iam), ACIS (.sat,.sab)
Mesh
STL (.stl), OBJ (.obj), Polygon File Format (.ply), 3D Manufacturing Format (.3mf)
CAE
Abaqus(*.inp), ANSYS (.cdb, .msh, .rst, .rth, .cas, .dat), LS-DYNA (.k) NASTRAN (.bdf, .op2), Patran(.pat), CGNS, (.cgns), Universal File Format (.unv), Topology Optimization Result (.op2)
Slice
Common Layer Interface (.cli)
Other
Bitmap (.png), Point Data (.csv), Vector and Scalar Point Maps (.csv), Voxel Grid (.vdb)
Generate
Create high-performance geometries.

Lattice Structures
Volume and surface lattices. Graph, TPMS, and custom unit cells. Stochastic structures. Rib grids.
Topology Optimization
Multi-objective and multi-constrain optimization. Automated post-processing.
Advanced Modeling
Variable shelling and offsets. Fillets and smoothening. Boolean operations.
Design Analysis
Built-in structural and thermal FEA. Import, conversion, and exchange utilities.
Build Preparation
Part orientation. Support structure generation.
Export
Convert to the format you need.

CAD
STEP (.step), Parasolid (.x_t and .x_b), IGES (.iges)
Mesh
STL (.stl), OBJ (.obj), Polygon File Format (.ply), 3D Manufacturing Format (.3mf)
CAE
Abaqus (.inp), ANSYS (.cdb), Nastran (.bdf), LS-Dyna (.k), Universal (.unv), Patran (.pat), Fluent (.msh)
Slice
Common Layer Interface (.cli), Common Layer File (.clf), Renishaw Point Data (.csv), Renishaw CLI (.cli), Arcam ABF (.abf), Stratasys Layer (.ssl), EOS CLI (.cli), BW image stacks (.png), 3D Systems (.slc), ConceptLaser Slice v4 (.cls)
Other
nTop Implicit File (.implicit), Point Data (.csv), Vector and Scalar Point Maps (.csv), Voxel Grid (.vdb)
Integrate
Integrate with your existing software stack.

nTop Automate
Using nTop Automate, you can write custom code to execute nTop workflows through a programmatic environment.
PLM
Leverage reference integrations and the nTop PLM connector to integrate nTop into your system.
MDO
Integrate with popular multidisciplinary design optimization platforms, including ModeFrontier, ModelCenter, and ProcesComposer.
Driving innovation
For Fortune 100 companies, innovative startups, and everyone in between.

Related resources
Ready for the next step?
See for yourself why leading companies in the aerospace, automotive, medical, and consumer industries have chosen nTop as their engineering design software solution.