Full-flight qualification for F-16 aircraft spare part in just 30 days
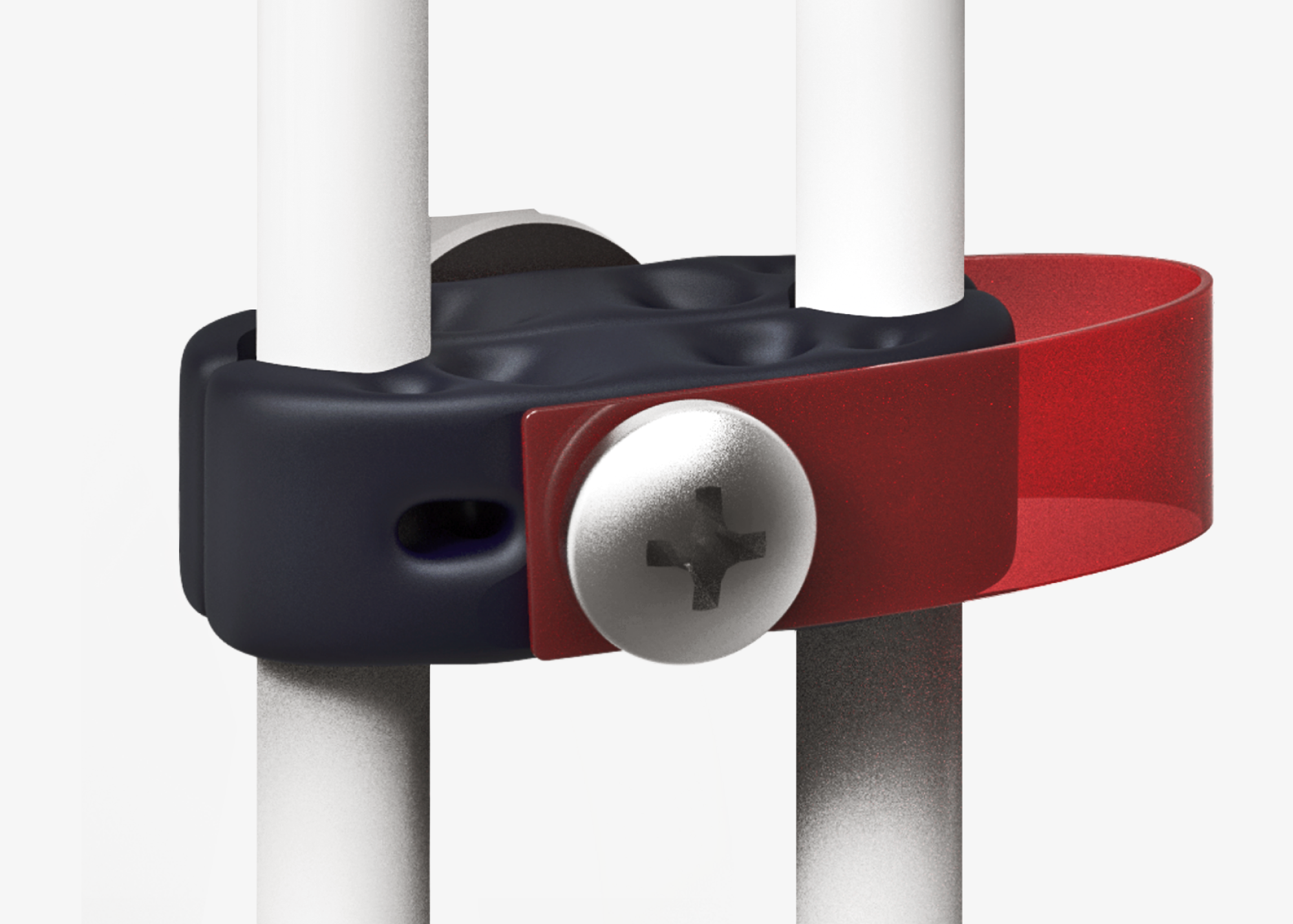
Applications
Key Software Capabilities
- Design automation
- Simulation
- Topology optimization
Summary
Engineers used nTop to redesign a family of F-16 aircraft hydraulic tube clamps for AM as participants in an advanced engineering competition. The final part was 2x stiffer and manufacturable on demand.
The project
Design a stronger, more durable hydraulic line clamp
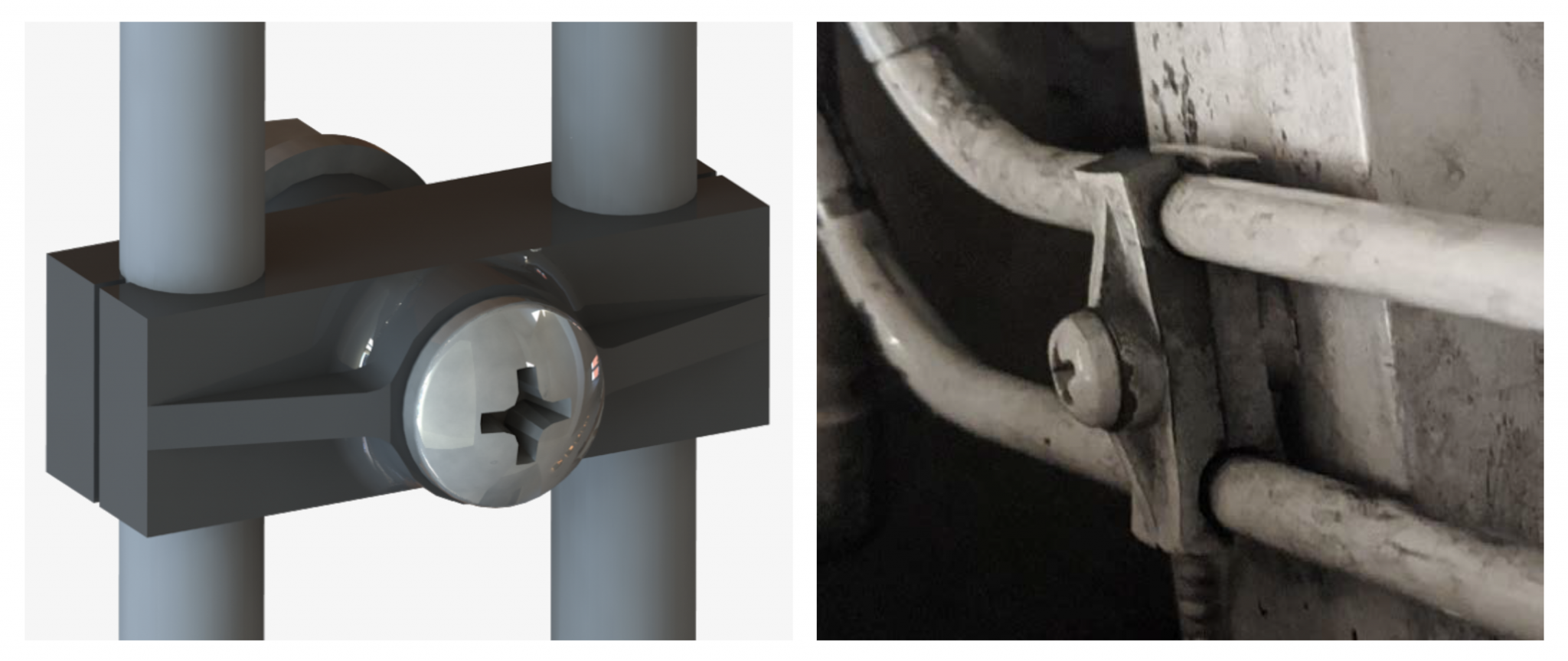
The legacy design from 1966 of the hydraulic tube clamp part family. Exact loading conditions were unknown.
The U.S. Air Force’s Rapid Sustainment Office (RSO) held an advanced engineering competition where teams were presented with some of the Air Force’s most pressing technical problems. This year’s challenge in the Approval Sprints category: produce a stronger, more durable hydraulic line clamp for the U.S. Air Force’s fleet of F-16 aircraft.
The new design must have the same level of performance as the original, and should be able to be rapidly deployed.
The challenge
Overcome the limitations of traditional manufacturing.
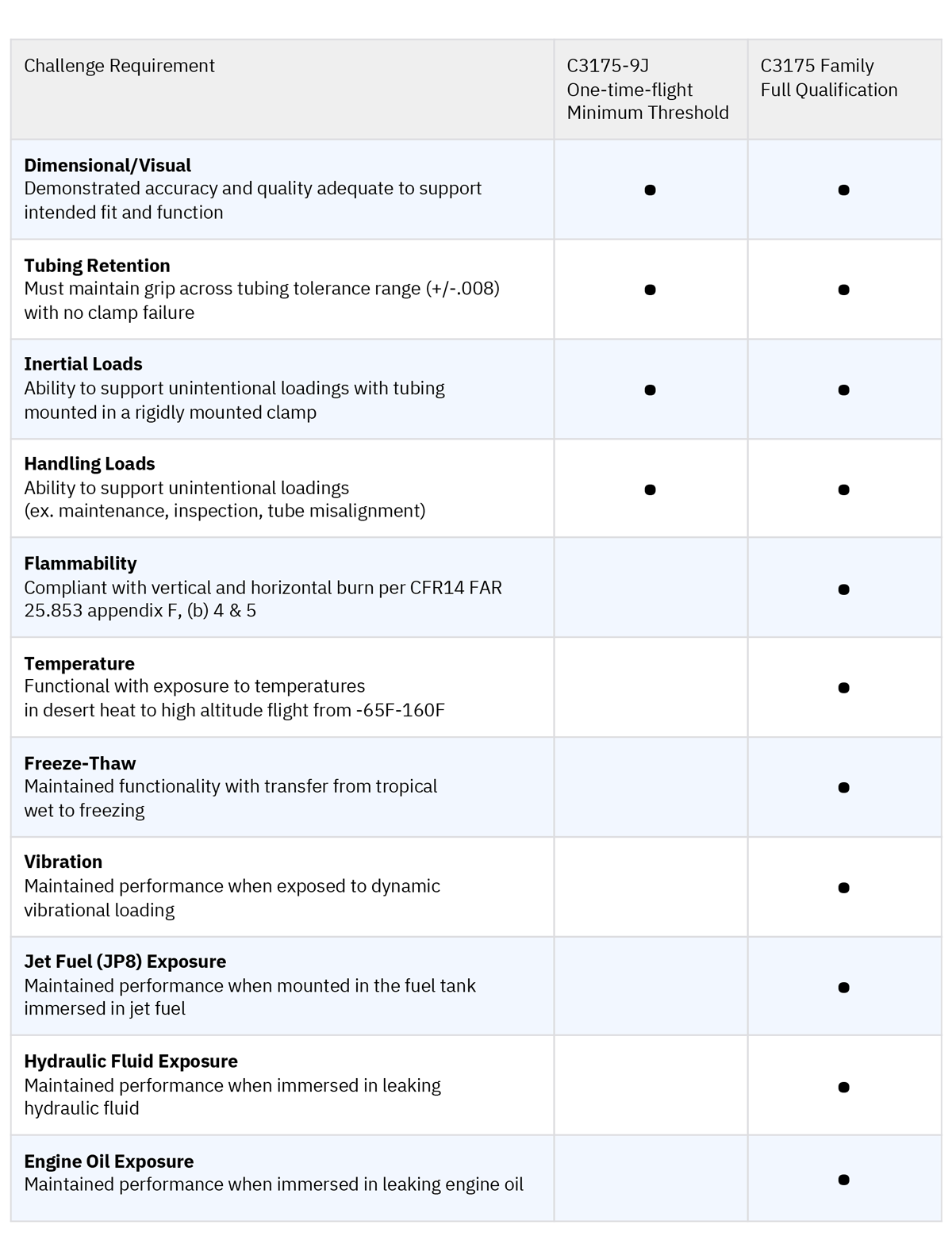
The list of design requirements presented by the RSO. The team managed to pass the full qualification criteria in less than 30 days.
The US Air Force has thousands of hydraulic tube clamps in use. The clamps fail over time due to exposure to vibrations, chemicals, and heat — replacement parts must always be on hand.
By digitizing supply chains, the Air Force can overcome the limitations of traditional manufacturing. In this case, the old design was either CNC machined from a material that produced toxic fumes, or injection molded with long lead times at high storage costs.
The solution
Create a stiffer, lighter design in three parts.
The new design has three parts: two clamp halves and a flexible tether.
They started by first reverse-engineering the legacy clamp to identify loading conditions.
They used topology optimization in nTop to visualize the load paths. Then they drafted possible solutions in CAD and evaluated their performance with FEA. nTop’s smoothing functionality helped to further boost performance.
Finally, they 3D-printed samples of the clamp for testing and validation.
The results
2x
Stiffness
5%
Weight reduction
50%
Reduction in peak stresses after smoothing
30
Iterations in 30 days
Why nTop?
nTop enabled engineers to quickly iterate on their new design with reusable workflows. Automated smoothing greatly reduced peak stresses — without user input. Simulation capabilities helped to speed up the development process.
Reusable workflows
When new experimental results became available or when fundamental changes needed to be made to the design, the engineers quickly generated new geometry simply by altering the inputs of their workflow in nTop. This enabled the team to kickstart a new iteration of analysis, evaluation, and testing at a speed that would be impossible if they’d used only traditional CAD software.
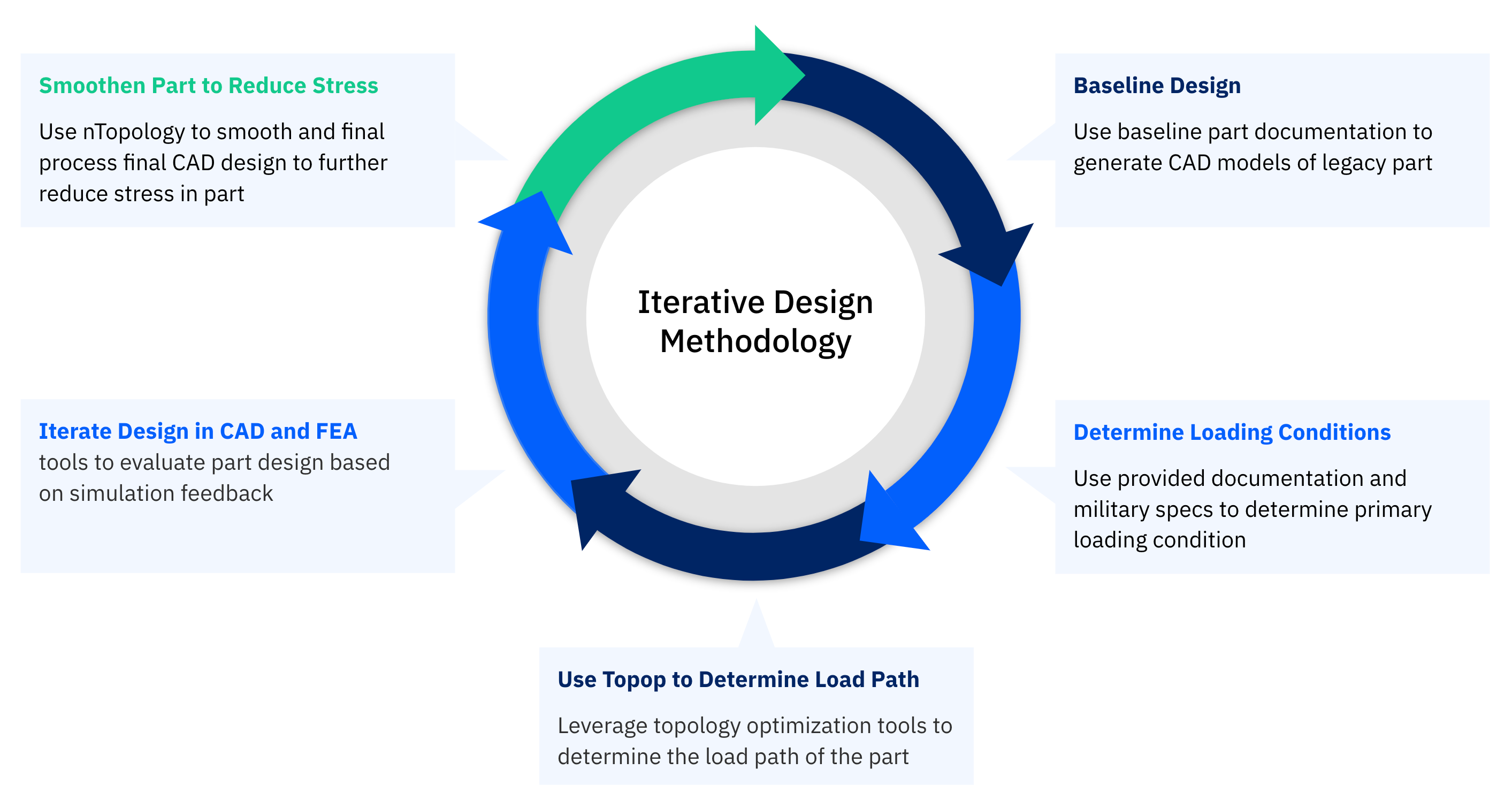
The team evaluated over 30 designs in 30 days. This was only possible due to the reusable design workflows they created using nTop.
Automated smoothing
In addition to using topology optimization to identify the loading paths, the team took advantage of nTop’s automated smoothening capabilities to post-process the geometry. The result: 50% reduction in peak stresses. This post-processing step was carried out without user input.

The final clamp design
Simulation
The team used simulation to test the candidate solutions for fatigue strength, grip force, pull-out breaking force, and behavior during take-off and landing. These simulations enabled them to limit experimental validation steps to a minimum, accelerating their development process.
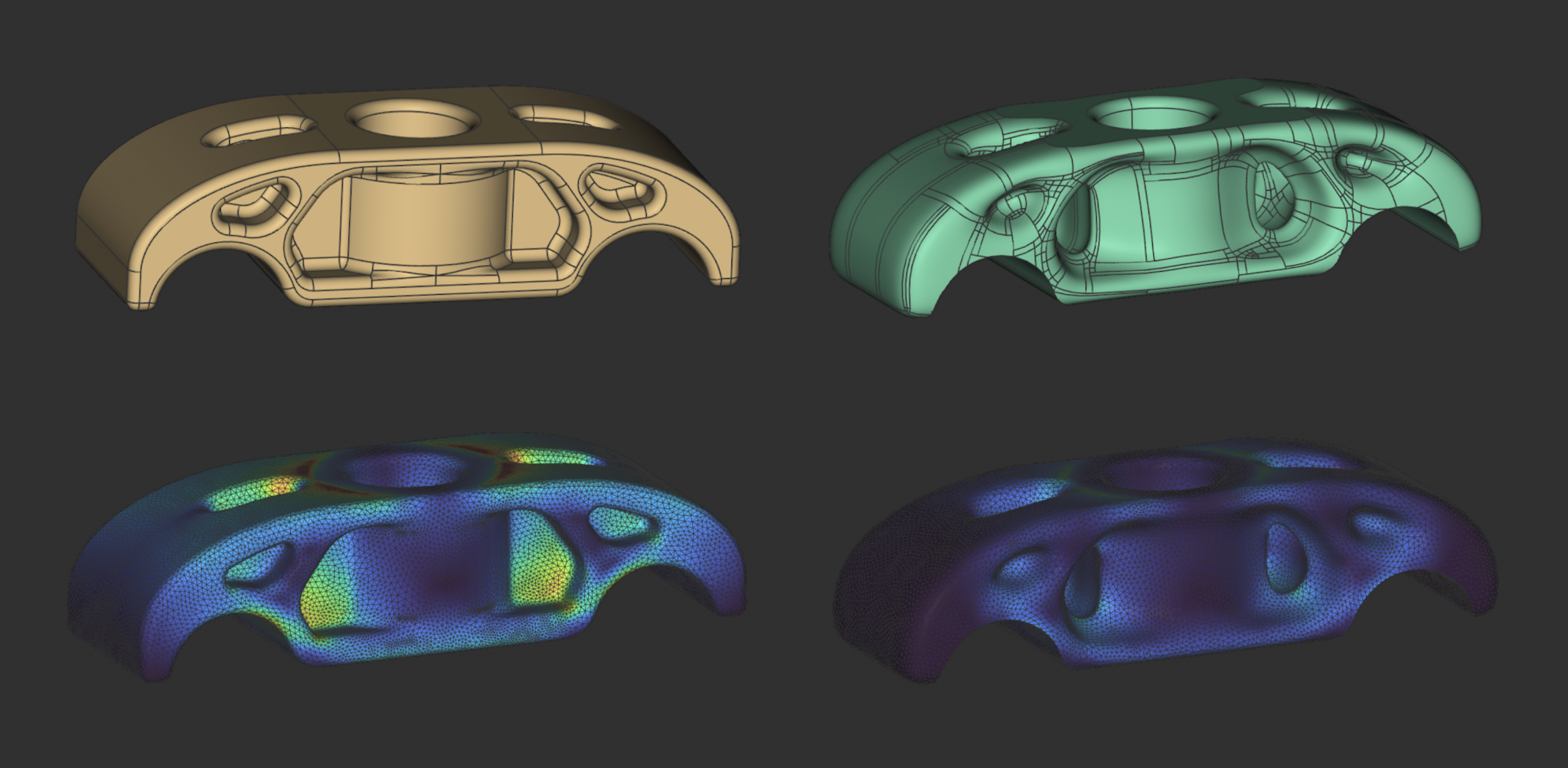
Smoothening the topology optimization results provides a significant reduction in stresses.
Conclusion
Through design optimization and automation, nTop made it possible to design F-16 aircraft hydraulic tube clamps that could be additively manufactured. The team created a lighter, more efficient clamp that saved time in the manufacturing process.