Lightweight and cut costs of 3D printed orthotics and prosthetics
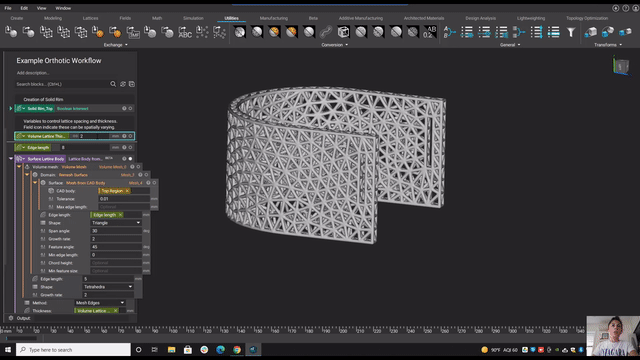
video: Lightweight and cut costs of 3D printed orthotics and prosthetics
Published on July 12, 2021
Applications
Key Software Capabilities
- Surface textures
Custom orthopedic devices, such as orthoses and prosthetics, are expensive to manufacture using traditional means. By digitizing your design and manufacturing using 3D printing processes, you can minimize manual labor, cut costs, and scale your production.
In this nTop Live, Gabrielle Thelen, application engineer at nTop, shows you how to apply different design approaches to reduce weight, increase patient comfort and improve overall ergonomics, breathability, and aesthetics of an AFO (Ankle Foot Orthosis).
She uses volume lattices and structural ribbing to lightweight various features of the AFO by spatially varying the density and thickness of the lattice beams and ribs. The result is a 53% weight savings between the original design and the new one.
Watch and learn how to:
- Reduce the weight of 3D printed prosthetics & orthotics
- Spatially control important design parameters using field-driven design
- Calculate mass and weight saving of the original design to the optimized design
Download the files
Recreate the steps that Gabrielle followed in this nTop Training. To download all the necessary files for this training, please see this link.
Related content
- VIDEO
When your design changes, how fast can you respond?
- CASE STUDY
Replacing spacecraft supermaterial with high-performance lattice
- VIDEO
Creating a computational design workflow to lightweight drone panels with nTop’s new ribbing tools
- WEBINAR
Accelerating Product Engineering with Computational Design
- CASE STUDY
Reducing weight to help win and withstand the rigors of a 24 hour Le Mans race