Functional lightweighting and conformal cooling of metal 3D printed aerospace part
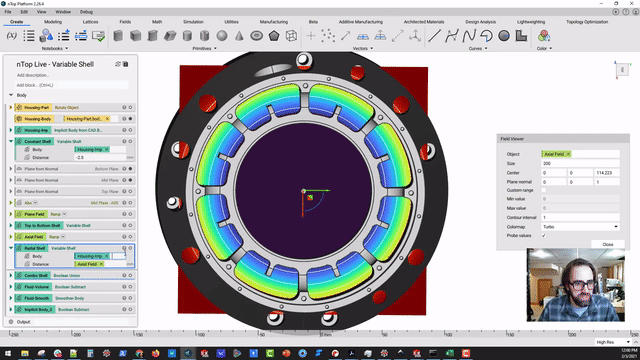
video: Functional lightweighting and conformal cooling of metal 3D printed aerospace part
Published on February 3, 2021
Applications
Key Software Capabilities
- Simulation
By following functional lightweighting best-practices, not only can you significantly reduce the weight of an additively manufactured part, but you can also consolidate multiple capabilities into a single component.
In this nTop Live, Ryan O’Hara, Technical Director of Aerospace and Defense at nTop, shows you how to apply practical lightweighting techniques on an aerospace component. As an example, he uses the housing of a microturbine generator and removes material from its shell to create conformal cooling channels.
Watch and learn how to:
- Leverage variable shelling to remove material from non-load-bearing areas
- Apply automated smoothening to prepare the part for additive manufacturing
- Reduce the temperature of a component using fuel as the heat-transfer medium