Multifunctional optimization of a next-gen robotic end effector
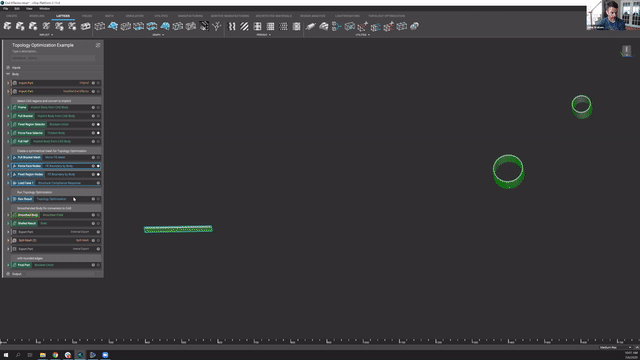
video: Multifunctional optimization of a next-gen robotic end effector
Published on July 6, 2020
Additive manufacturing has opened a whole new design space for creating robotic end effectors and flexible grippers that conform to the shape of the objects they pick up.
In this nTop Live, we show how flexible lattice structures can be used to improve the grip of a robotic system. We show how to reduce it's mass using topology optimization and how to transfer your nTop designs back to your CAD or PLM system.
Watch and learn how to:
- Set up a DoE to achieve the desired flexibility and compliance
- Use topology optimization to minimize mass while maintaining strength
- Export the optimized part back into the assembly of your CAD software
Download the files used in the session here.