SI-BONE scales implant design with batch processing

Applications
Key Software Capabilities
- Design automation
- Lattice structures
Summary
SI-BONE developed a novel osseointegrative lattice structure and used nTop’s design automation to apply it to a product family with 70+ unique parts in under six hours — with full traceability.

About: SI-BONE is a global leader working to make sacropelvic conditions universally recognized, and to treat them effectively through innovation, evidence, education, and advocacy.
- Industry: Medical
- Size: 300+ employees
- Location: Santa Clara, CA
- Application: Architected materials, Mass customization
The project
Mass customize an implant family with 70+ configurations

SI-BONE’s family of 3D-printed spinal implants featuring an osseointegrative lattice design.
SI-BONE needed to mass-customize and automate the design of a spinal implant product family with 70+ unique part configurations.
The implant needed to mimic the properties of cancellous bone to help improve patient outcomes.
The design and manufacturing process also needed to be quick and error-proof.
The challenge
Automate mass customization to save engineering time
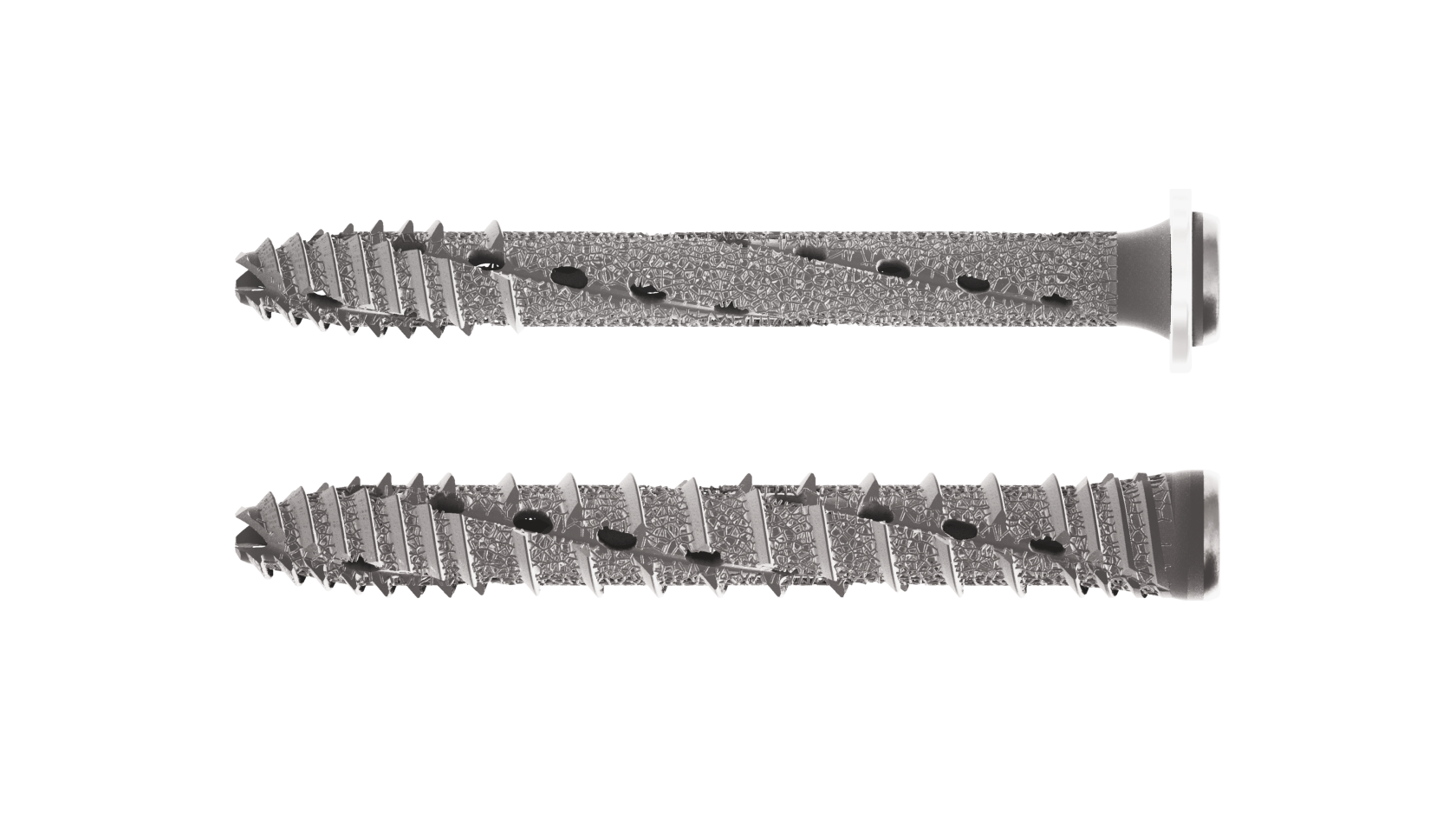
The family of 3D-printed implants includes more than 70 unique part configurations.
When done manually, processing the implants is costly and time consuming, typically taking up to 12 invested engineering hours for a single batch of implants.
Entering the data manually is also prone to human error, which increases operational risk.
The solution
Create a repeatable batch-processing workflow with nTop Automate.
To automate this step, SI-BONE used batch processing with nTop Automate. With a simple script, they applied the new lattice design to the whole product family in just under six hours. They were also able to run the automation without any human intervention, saving considerable engineering time.
This repeatable process enabled the team to create design workflows that are traceable and easy to maintain and saved thousands of dollars in operational costs for their business.
The results
90%
Reduction in operational costs
2x
Faster processing
91%
Reduction in invested engineering hours
3
Functions in a single part
Why nTop?
nTop’s ability to automate design workflows and mass-customize products enabled SI-BONE to scale the production of their spinal implants. Further, nTop’s latticing capabilities made it possible for SI-BONE to create an osseointegrative design that mimics the properties of bone, and helps to improve patient outcomes.
Design automation
Scaling design processes using traditional tools can be time-consuming and prone to errors.
To tackle this challenge, SI-BONE used nTop to develop and automate design workflows. They automatically applied their standardized osseointegrative structure to a product line of more than 70+ parts overnight with a simple script. Using batch processing, they saved hours of engineering time and thousands in operational costs.

Overview of the basic steps of the design workflow during the development phase
Osseointegrative lattice design
With nTop, SI-BONE explored multiple design variations of a highly porous trabecular structure. By adjusting critical parameters of their workflow, they controlled every aspect of the lattice beams, including beam thickness and pore size. They also introduced gradients to create a smooth transition between the highly porous lattice and the structurally critical solid regions of the implant.
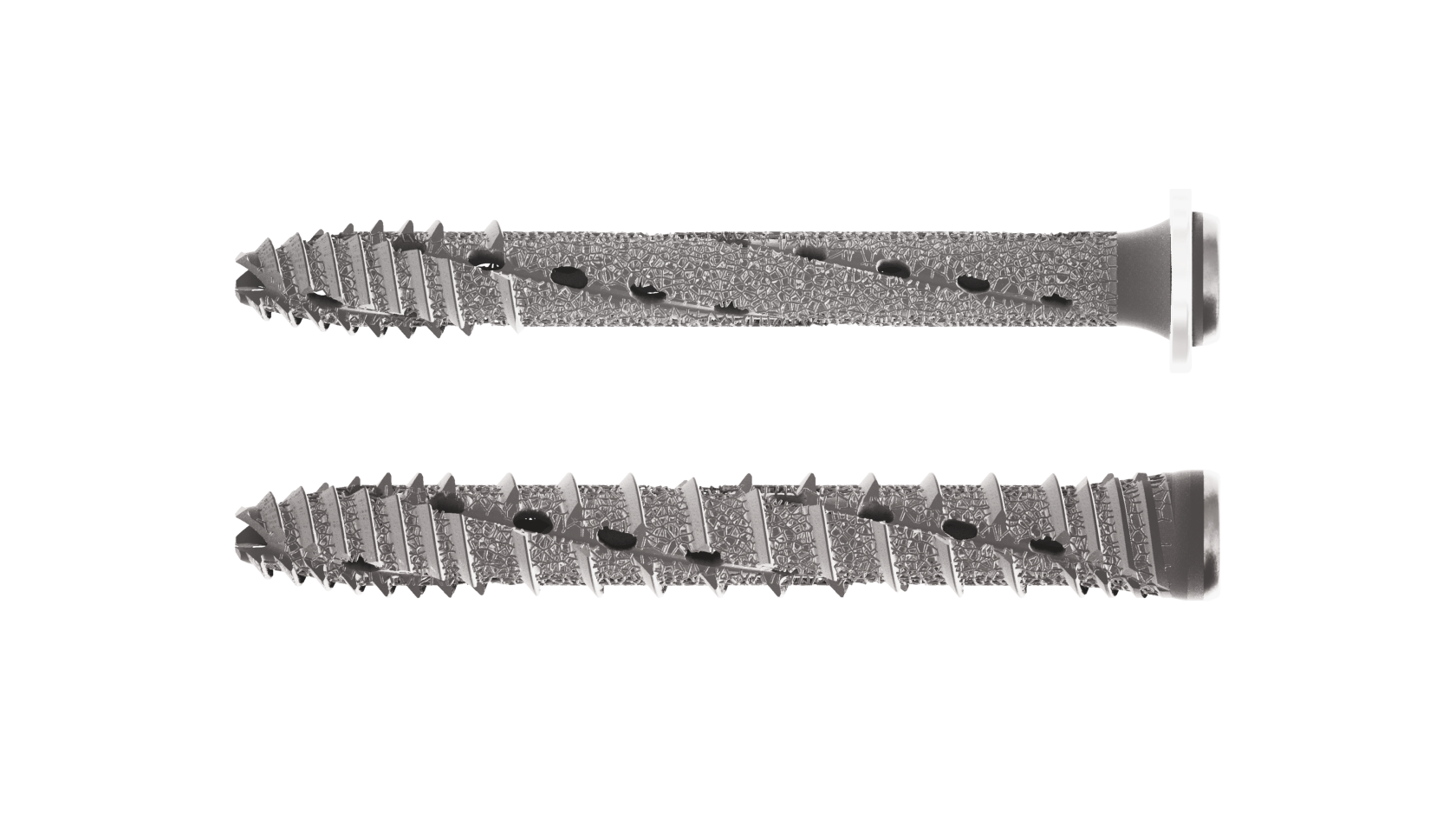
The osseointegrative lattice structure imitates the properties of bone.
Standardized workflow
To ensure their workflow would produce consistent results, the SI-Bone team generated a traceability report that recorded lattice properties like mass, surface area, and relevant mesh characteristics.
Then they packaged the workflow into a single custom nTop block so it could be shared with other nTop users and reused with full traceability.

Once the design workflow is complete, it can be packaged as a revision-control custom block.
Batch processing
Using nTop Automate, SI-BONE created a short Python script to batch process the whole product family.
It took about one hour of engineering time to create the script and prepare CAD data for processing and six hours of unsupervised computing time to execute it on more than 70 unique part configurations — averaging three to four minutes per part.
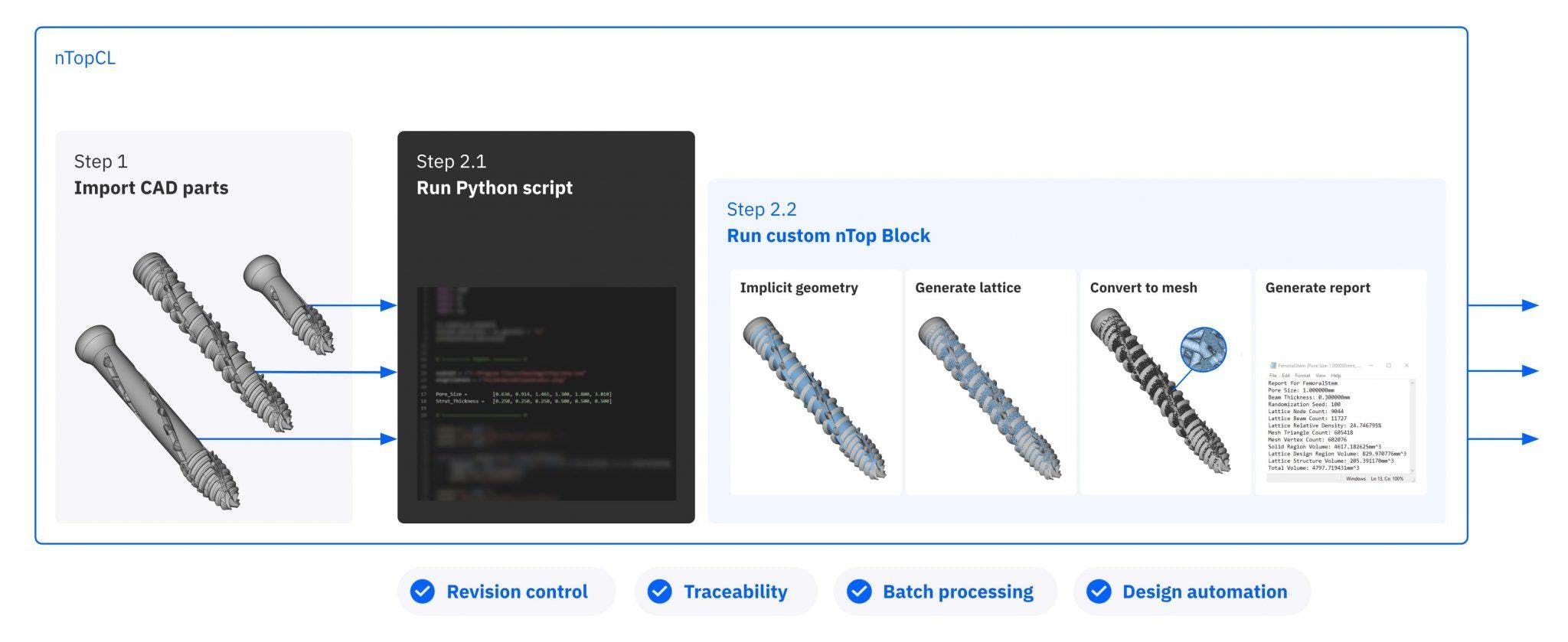
Batch processing with nTop Automate automates the time-consuming step of manual data processing.
Conclusion
With nTop, SI-BONE halved their computational processing time, achieved 100% accuracy with their automated results, slashed operational costs by 90%, and removed bottlenecks in product development.