The opportunities and challenges of design for metal additive manufacturing by Tim Simpson of Penn State
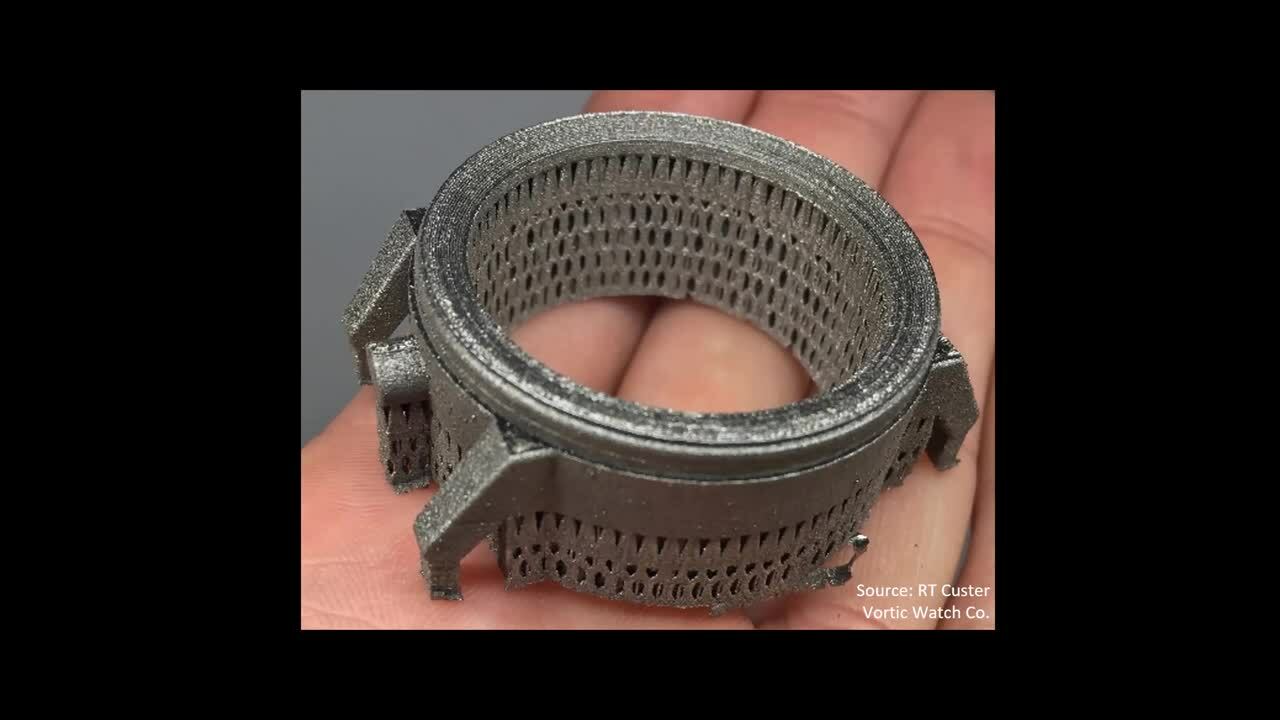
video: The opportunities and challenges of design for metal additive manufacturing by Tim Simpson of Penn State
Published on August 18, 2020
Timothy Simpson, Penn State Univerity and The Barnes Global Advisors
Anyone can buy an additive manufacturing (AM) system, learn how to run it, and make a part. Understanding how to use design to innovate with AM and overcome its limitations are essential to differentiating yourself from others, and designing for metal AM is key to making a successful business case. The design challenges companies face as they progress from part identification to part modification to part optimization with AM will be discussed along with the implications of design for AM on component cost, lead-time, and performance using examples from a variety of industries.
Key takeaways:
- How design can be used to innovate with AM and overcome the limitations of AM
- The progression of DFAM from part identification to modification to
- The implications of DFAM on component cost, lead time, and performance