From implicit to print without making a mesh

Written by Daeho Hong | Product Manager (Integrations) at nTop
Published on November 10, 2022
As technology advances, limitations of legacy systems become more apparent. With the increase in design complexity, the weakest link in many additive manufacturing (AM) workflows today is the technology used to transfer design data between systems. Here’s how we can bypass this roadblock.
Interoperability is the capacity to exchange and communicate data between systems and is much more common in our daily lives (and a lot more important) than you may think. Yet, we mainly feel its impact when things don’t work as they should.
Today in engineering design, data exchange is becoming a bottleneck in many AM product development initiatives. Our current mechanisms create many practical challenges when transferring intricate designs between software and hardware systems — and, in extreme cases, make data exchange basically impossible.
In this article, we explain why we need new data exchange mechanisms and what is our approach to solving this problem. Also, we show you the results of our recent collaboration with EOS to manufacture a previously unprintable large industrial heat exchanger designed by Siemens Energy.

Direct data exchange connection prototype between nTop and EOSPRINT.
What’s wrong with the current solutions?
Since the ’80s, manufacturing has become far more advanced. Today, automated systems can create products at higher throughput and better quality. Additive manufacturing has become a key part of the manufacturing ecosystem for its ability to produce parts with intricate features that are impossible with conventional manufacturing.
At the same time, advanced engineering design software, like nTop, empowers engineers to take advantage of the design freedom unlocked by AM technologies and develop the next generation of high-performing products.
While the file formats used to exchange data between design and manufacturing have served us well, they haven’t changed much. These are either based on discretized geometry, like the STL mesh, or boundary representations, like the STEP file. All these formats were developed for a different era when subtractive manufacturing was the only option. Today, part designs for additive manufacturing can be far more complex and have up to 1000x more features.
While working with many nTop users — engineers from the aerospace, automotive, medical, and consumer industries who are developing the most advanced AM products currently in production — we identified certain limitations inherent to the current generation of data exchange mechanisms that bring many projects to a halt.
When scaled to meet the current engineering product development needs, the existing solutions result in files that are:
- Huge — often in the multiple gigabyte range
- Wasteful — taking hours of high computing power to generate, open, and process
- Inaccurate — since they are approximations of the actual design
At nTop, we support the conversion to these data formats and continue to invest heavily in improving the speed and accuracy of mesh and b-rep generation. However, we feel there is a better solution for the AM industry — and this is a notion shared by other leaders in this ecosystem, like EOS, our partner in this prototype project.
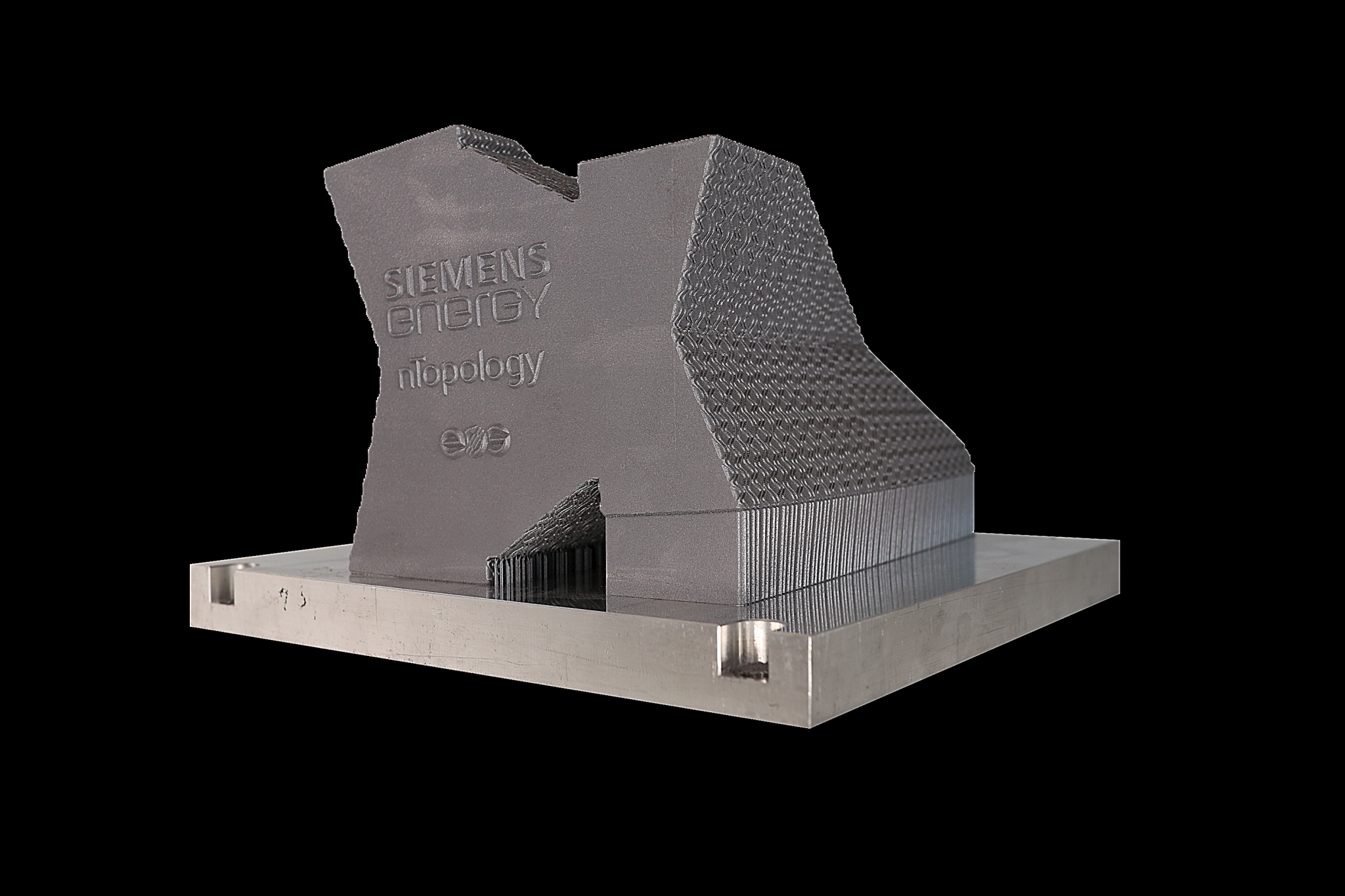
This industrial heat exchanger was designed by Siemens Energy in nTop. The design was previously unmanufacturable due to the limitations of the current data transfer formats.
What is implicit interoperability?
Simply put, implicit interoperability is the direct transfer of implicit geometry between design, build preparation, CAD, CAE, PLM, and visualization software without any loss of geometric precision or design intent.
From a technical perspective, there are many ways to achieve this goal. If you want a more in-depth view of one of the possible implementations of implicit interoperability and some earlier examples, you can read our article on CodeReps.
We believe that implicit modeling is essential to taking full advantage of additive manufacturing. Implicit interoperability removes frictions related to generating, transferring, and processing large and intricate mesh files—an issue that bedeviled the AM industry in recent years. More specifically, this method of exchanging design data is:
- Compact — the files are only a few kilobytes in size and are generated in seconds
- Precise — they are lossless representations, not mesh approximations
- Intelligent — as it supports full parametric editing, not just "dumb solids”
Proof of concept: Large industrial heat exchanger
Let’s now take a closer look at how we put theory into practice. For this prototype, we collaborated with EOS to create a direct implicit connection between nTop and EOSPRINT.
The goal was to manufacture a previously unprintable industrial heat exchanger designed by Siemens Energy.

The manufactured heat exchanger on the build plate. The design was section-cut to reveal the internal geometry of the core.
Ole Geisen, Head of Engineering Services for Additive Manufacturing at Siemens Energy, explained their issues with innovating heat exchangers using AM, “File size hasn’t been much of a challenge in the past. However, with the industry’s advancements regarding topology optimization, generative design, and DfAM, part geometries are getting increasingly complex. As a result, exchanging such complex geometries with traditional data formats is becoming more challenging, severely hindering thermal management innovation.”
Due to its intricate internal structure and enormous size, this design could not be meshed and manufactured without spending weeks of processing time for mesh generation, build preparation, and slicing. Moreover, the resulting data would be extremely large, making its management and processing immensely time-consuming.
Prototype: From implicit to print
First, the heat exchanger was designed in nTop. It features a core consisting of wavy surfaces that promote heat transfer and an external gyroid-based rib grid to increase the design’s stiffness while keeping it lightweight.
The original design was approximately one meter in length. However, for this demonstration, the design was manufactured at a 25% scale (220 x 150 x 160 mm) to fit in the build volume of the EOS 290 system.

Section cut of the heat exchanger design in nTop. The pathways for the hot and cold fluid domains in the heat exchanger core are visible.
Then, the design was exported from nTop in an implicit data format. The file was less than 1 MB and generated in mere seconds. The support structures were also created in nTop and exported as mesh files.
Next, the heat exchanger design and the supports were directly loaded into EOSPRINT, where they were sliced at the optimal accuracy of the AM system.

The design was imported into EOSPRINT in an implicit format and sliced for manufacturing.
Finally, the heat exchanger was manufactured on an EOS M290 machine. With the progressive slicing capabilities of EOSPRINT software, once enough layers were generated, we could start the build. EOSPRINT continued slicing and fed the printer with new slice data as computed.

The manufactured heat exchanger on the build plate (left) and comparative table with statistics on data transfer.
What’s next?
Implicit interoperability is a field of active research at nTop. Our vision is to remove any blockers in implicit data exchange. We are working with partners — other leading companies in the ecosystem — to develop implicit interoperability capabilities that empower our users to choose the best tool for transferring design data between software and hardware systems.
The direct connection between nTop and EOSPRINT is currently in a pre-beta stage. However, we are working actively to push this capability to a public release.
Beyond this project, we have created prototype implicit connections with other types of software, including traditional CAD (Siemens NX), CAE (INTACT.SIMULATION), and visualization (Zea 3DXP).

Direct implicit data transfer is only one example. We have developed other implicit interoperability prototypes for other relevant engineering use cases.
Call for partners
Are you interested in collaborating with us to further develop this technology? Let's work together to create the future of additive manufacturing data exchange. Contact us today.

Daeho Hong
Product Manager (Integrations) at nTop