Introducing nTop 4: Realize the full potential of additive manufacturing

Written by Trevor Laughlin | VP, Product at nTop
Published on April 14, 2023
Additive manufacturing has unleashed a whole new world of design freedom, making it possible to produce complex parts that offer breakthrough levels of performance. But this complexity creates bottlenecks throughout the product development process -- from design to manufacturing. Over the past few years we’ve worked closely with industry leaders across the aerospace, energy, mobility, and medical sectors to develop a suite of new product capabilities that allow them to achieve new innovations and propel their AM applications forward into mainstream production.
Today we are excited to introduce nTop 4, the next major release of our software, purpose-built to harness the vast design options enabled by additive manufacturing. nTop 4 allows you to bring a new generation of products to market even faster.
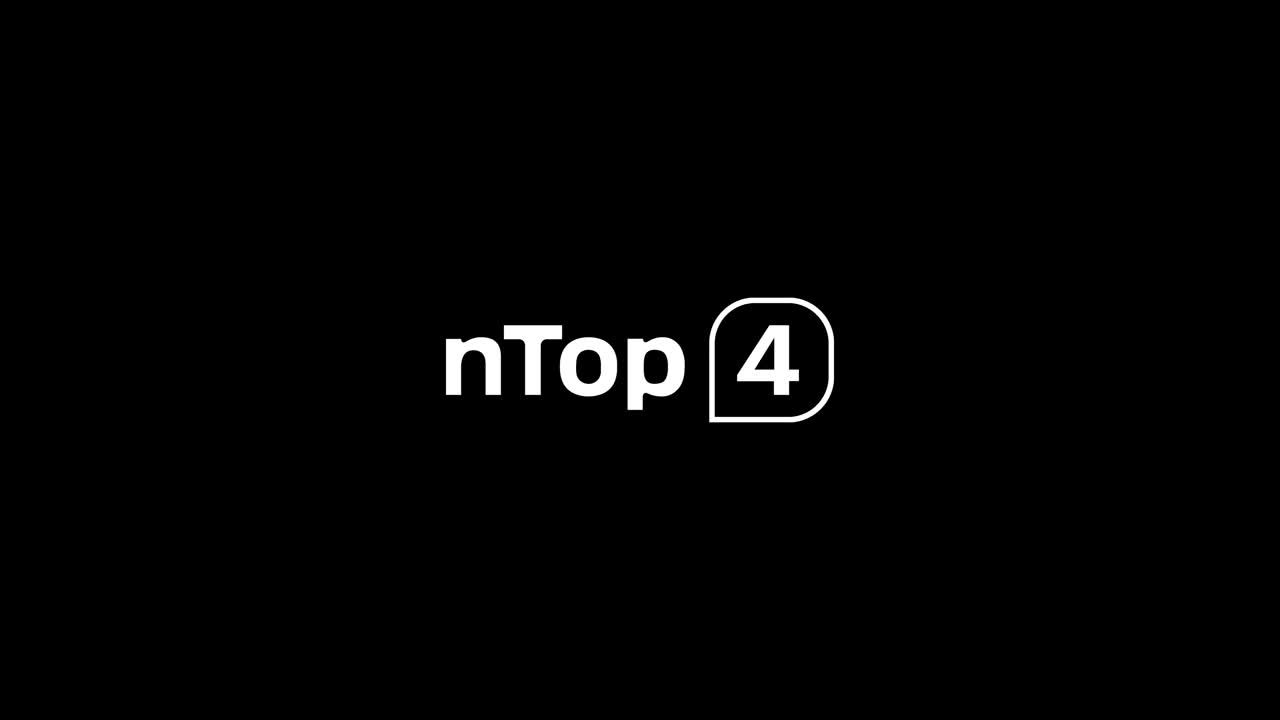
nTop 4 video
Turn design complexity into a competitive advantage with Field Optimization
As AM technology has matured, so has the sophistication of the problems engineers are trying to solve. It’s easy to create complex geometry (for us 🙂), but successfully turning that geometry into highly engineered, production-quality parts demands much more. The design freedom enabled by AM coupled with complex engineering requirements makes it impractical or even impossible to design these types of parts manually. Without being able to fully utilize the design space, engineers are leaving performance on the table in applications where performance matters most. In traditional CAD, the approach might be to make a parametric sketch of a few key design variables – but how do you parameterize geometry where every point in space can be optimized?
In nTop 4, we’re introducing a new capability called Field Optimization, which is a multi-objective, multi-scale, and closed-loop optimization capability that is a more effective and efficient way to design complex, high-performance parts. The approach relies on a novel combination of our implicit modeling technology, Field-Driven Design approach, and a generalization of our existing topology optimization framework. This new capability allows engineers to focus on specifying the design intent and requirements of the part while letting the software automatically determine the complex geometric details such as lattice layouts, wall thicknesses, rib patterns, and/or other spatially-varying parameters.
The use of Field Optimization is similar to that of traditional topology optimization. The most noticeable difference is that the underlying “material model” used to compute the properties of the structure is now a function of any number of geometric design parameters, rather than just a single value, such as material density. For example, to optimize a satellite bracket for the NASA EXCITE challenge we started by using a traditional topology optimization to get the global shape and then subsequently applied a “shell and infill” optimization to further optimize the weight and stiffness of the part. This resulted in a part that was twice as durable under vibration loading conditions (the driving requirement for this part) while still coming in 6% lighter than alternative approaches used to date.

Applied to the NASA EXCITE bracket, Field Optimization simultaneously optimized weight and vibrational stiffness by fine tuning the local wall and gyroid thickness throughout the part.
A second application of Field Optimization is the design of a hip implant engineered to fuse with bone. In order to generate a comfortable implant that lasts a long time, you need the effective mechanical properties at the surface of the implant to match that of the bone to reduce stress shielding effects. Here we used numerical homogenization to derive an analytical relationship between multiple design parameters for the variable cellular structure and its expected mechanical properties (e.g., stiffness, relative density, etc.). Using a methodology describing the stress shielding effects[ref], it took roughly one hour to build a Field Optimization workflow in nTop 4 and achieve a lighter weight implant with a better biocompatibility profile resulting in reduced fatigue and increased longevity.

Applied to a hip implant, Field Optimization simultaneously optimized for strength, weight, and bone-like properties by locally optimizing the cell size and thickness of the Voronoi cells.
Today, in nTop 4, we’ve released easy-to-use optimization workflows for highly engineered applications in lightweighting, architected materials, and industrial design. Additionally, the open architecture allows advanced users to develop custom material models built on their own numerical, experimental, and/or analytical data. Looking forward, we are already exploring new applications in thermomechanics, fluid flow, acoustics, and electromagnetics. We believe Field Optimization is the future of generative design and will be relevant for optimizing any high-performance part in the future, whatever the manufacturing method.
Learn more about Field Optimization.
Eliminate data exchange bottlenecks for even the most complex designs with Implicit Interop
We know that for engineers using nTop, the job isn’t done until a physical part can be reliably produced and performs as expected. That’s why our job doesn’t end with design but extends into manufacturing by ensuring parts designed with our lightweight and easy-to-manipulate implicit models can be easily produced.
Industrializing AM is no longer limited by design or manufacturing, but rather, the data transfer between them. Typically, designs are exchanged to printers and other engineering applications using discretized mesh file formats like *.STL. These files are large and difficult to manage, they take a long time to generate, and they compromise the accuracy of the part. For geometrically complex designs such as those enabled by Field Optimization meshing is sometimes even impossible.
With nTop 4, we are excited to formally launch Implicit Interop to ensure engineers using nTop have a reliable and feasible path to production, even for their most complex designs. With Implicit Interop it is now possible to directly exchange nTop geometry in a compact file format (a new *.implicit extension you’ll see in the software) which can be read and queried by other tools using a lightweight library that we now are making available to partners. With Implicit Interop, exchanging complex design data is now measured in the kilobytes to megabytes, not gigabytes.
Today, this capability is being introduced in the form of two new products:
First, we’ve connected with EOS to launch the nTop Plugin for EOSPRINT which allows our mutual customers to directly import, setup, and print nTop designs on EOS printers natively from EOSPRINT software. This plugin goes live in EOSPRINT 2.14, scheduled for release in June of 2023. If you are interested, you can test this today.
With this new capability we’ve seen complex designs that used to take days to mesh and slice load in EOSPRINT in minutes, allowing slicing to be done on-demand during the manufacturing process to achieve the optimal accuracy of the AM system.

Using the nTop Plugin for EOSPRINT, you can directly import complex nTop designs into EOSPRINT without having to deal with the challenges of mesh-based data transfer. This will become available with EOSPRINT 2.14 due to be released in June 2023.
Second, we are introducing nTop Core, a simple and lightweight library for our partners to open, use, and integrate nTop native geometry in their own tools and systems, enabling our customers to seamlessly integrate nTop into their own product development process, and ultimately use the best tool for the job.
This library is already powering the nTop Plugin for EOSPRINT. To test this further we collaborated with Inkbit who was able to independently incorporate the library into their software to read, query, and ultimately manufacture nTop parts directly from the *.implicit file itself (shown below), all without any meshing.

Using nTop Core, Inkbit was able to demonstrate the ability to read, query, and ultimately manufacture high-quality parts directly from nTop implicit files without any meshing.
In addition to these new capabilities, we are actively engaging with the 3MF community, working through how to exchange implicit data openly in 3MF. If you are a CAD/CAE/CAM software or hardware supplier interested in exploring how we might work together on Implicit Interop to benefit our shared customers and the industry at large, please contact us.
Learn more about Implicit Interop and other integration capabilities.
Multiply the impact of your engineers by deploying nTop Automate at scale
It’s almost never effective to just throw more engineers at a problem in order to solve it – rather, the most advanced nTop customers leverage the agility of additive manufacturing coupled with advanced design in order to multiply the impact of their engineers.
In order to deploy nTop at scale, we are launching a new product nTop Automate, allowing nTop workflows to be programmatically executed for use cases such as design space exploration, batch processing, and mass customization. With support for both Windows and Linux, customers can now deploy nTop workflows on more powerful computing hardware and/or cloud environments using more cost effective infrastructure.
Ocado Technology, for example, automated their part design and evaluation process allowing them to compress their prototyping cycle from months to a 3 week design sprint for the development of their new 600 Series Bot.
Lightforce Orthodontics uses nTop to automate a portion of their mass customization process, allowing them to efficiently scale a fully digital design process for a product that requires custom geometry for each set of braces.

Deploy nTop Automate to more efficiently scale your design and manufacturing throughput.
Deploying nTop Automate is a straightforward process. Whereas in existing engineering software it takes extra thought and tremendous effort to develop custom scripts and code, in nTop you are naturally building a fully-automatable program: simply define your key design variables and you have a packaged up design process that’s ready to go. Because nTop is built from the ground up on an implicit model, using this process to explore a design space or automate a mass customization process will be fast and reliable.
Learn more about nTop Automate.
Create value faster with our customer success programs
nTop 4 lets engineers realize the full potential of additive manufacturing, but we know that getting started can take time. In addition to delivering the best tools for the job, nTop offers programs to accelerate adoption and maximize impact in organizations of any size.
Today we are launching nTop Accelerate — a range of one-to-one training services, custom workshops, and design sprints — to help your organization best meet program objectives, and deliver value faster. Additionally, we are also continuing to invest in onboarding programs like nTop Learn, nTop’s online learning center, to ensure that engineers deliver value as fast as possible.
For more information on nTop Accelerate, contact your Customer Success representative.
Learn more about nTop 4
If you’d like to see these capabilities in action, watch our nTop 4 webinar recording or contact us for a demo.
With this new release, we’re officially changing our name to nTop. Learn more about why we’re making the change.

Trevor Laughlin
VP, Product at nTop
Trevor Laughlin is the VP of Product at nTop, where he is responsible for leading the product organization and vision, including product management, product design, and technical product support. Before joining nTop in early 2018, Trevor worked in the aerospace industry as a structural engineer and developed conceptual design software used by NASA. Trevor holds a Master of Science degree from Georgia Tech and Bachelor of Science from Iowa State University in aerospace engineering. He currently calls New York City home.